The Definitive Guide for Alcast Company
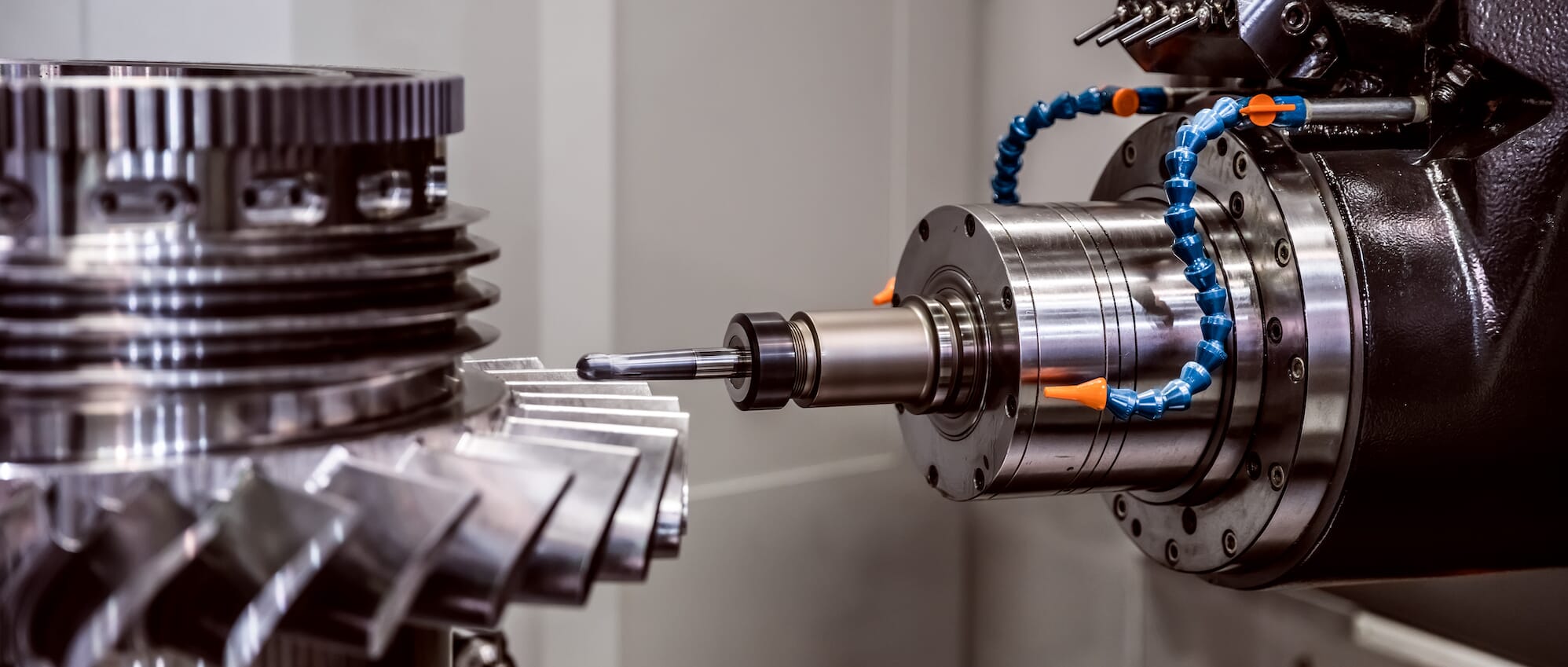
There are many minor distinctions between functioned and cast aluminum alloys, such as that cast alloys can contain more substantial quantities of other steels than functioned alloys. However one of the most notable distinction in between these alloys is the construction process whereby they will certainly go to provide the end product. Apart from some surface therapies, cast alloys will exit their mold and mildew in virtually the exact strong kind wanted, whereas wrought alloys will certainly undertake numerous adjustments while in their strong state.
If you believe that a wrought alloy might be the very best for your job, take a look at several of our write-ups that clarify even more regarding certain functioned alloys, such as Alloy 6061 and Alloy 6063. On the other hand, if you believe a cast alloy would be better for you, you can find out more regarding some cast alloys in our Alloy 380 and Alloy 383 posts (coming soon).
Alcast Company Things To Know Before You Get This

Having the experience and industry knowledge to craft your castings for optimum manufacturing and high quality outcomes will certainly streamline the project. Producing aluminum spreading requires a complex collection of procedures to achieve the appropriate outcomes. When determining on a brand-new aluminum foundry to partner with, guarantee they have extensive market experience and are well-informed about all facets of the aluminum spreading process: layout, production, material analysis, and item testing.
The smart Trick of Alcast Company That Nobody is Talking About
By selecting a firm who offers solutions that satisfy or exceed your item demands, you can be certain that your project will certainly be finished with the utmost accuracy and effectiveness. Certain light weight aluminum shops concentrate on certain sorts of making procedures or casting approaches. Different parts require different production techniques to cast light weight aluminum, such as sand spreading or die spreading.
Die spreading is the name provided to the procedure of producing complicated steel components via use mold and mildews of the part, additionally referred to as passes away. The procedure utilizes non-ferrous metals which do not include iron, such as light weight aluminum, zinc and magnesium, due to the preferable homes of the steels such as reduced weight, higher conductivity, non-magnetic conductivity and resistance to corrosion.
Our Alcast Company PDFs
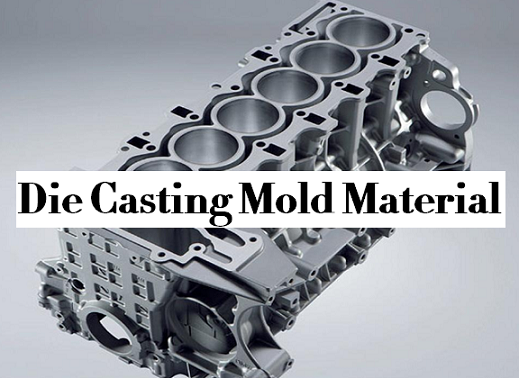
Despite the sub-process, the die spreading procedure can be broken down into 6 actions. After the pureness of the alloy is tested, dies are created. To prepare the needs casting, it is important that the passes away are tidy, so that no residue from previous productions stay. After cleansing, the ejection lubrication is used to the die to ensure a smooth launch.
The pure metal, likewise called ingot, is included in the heater and maintained the molten temperature level of the metal, which is then transferred to the shot chamber and injected right into the die (Aluminum Castings). The pressure is then kept as the steel strengthens. As soon as the metal solidifies, the cooling process starts
How Alcast Company can Save You Time, Stress, and Money.
The thicker the wall of the part, the longer the cooling time as a result of the quantity of interior metal that also needs to cool. After the element is totally cooled, the die halves open and an ejection mechanism presses the part out. Adhering to the ejection, the die is shut for the next injection cycle.
The flash is the added product that is cast during the process. Deburring eliminates the smaller pieces, called burrs, after the cutting procedure.
The Definitive Guide for Alcast Company
Nevertheless, this proved to be an incorrect test, since the tester could cut right into an item and miss out on a location with porosity. Today, leading producers utilize x-ray screening to see the whole interior of components important site without cutting right into them. This permits them to a lot more properly accept or decline parts. To obtain to the finished product, there are 3 primary alloys utilized as die casting product to pick from: zinc, aluminum and magnesium.
Zinc is one of the most secondhand alloys for die casting due to its reduced price of raw materials (Foundry). Its rust resistance also allows the elements to be long lasting, and it is one of the a lot more castable alloys due to its reduced melting point.
The Buzz on Alcast Company
As stated, this alloy is one of one of the most typically made use of, yet produces will, sometimes, select aluminum over zinc due to light weight aluminum's manufacturing advantages. Light weight aluminum is highly cost-effective and one of the extra versatile alloys. Aluminum is utilized for a number of different items and industries anything from home window frameworks to aerospace materials.
Comments on “The 8-Minute Rule for Alcast Company”